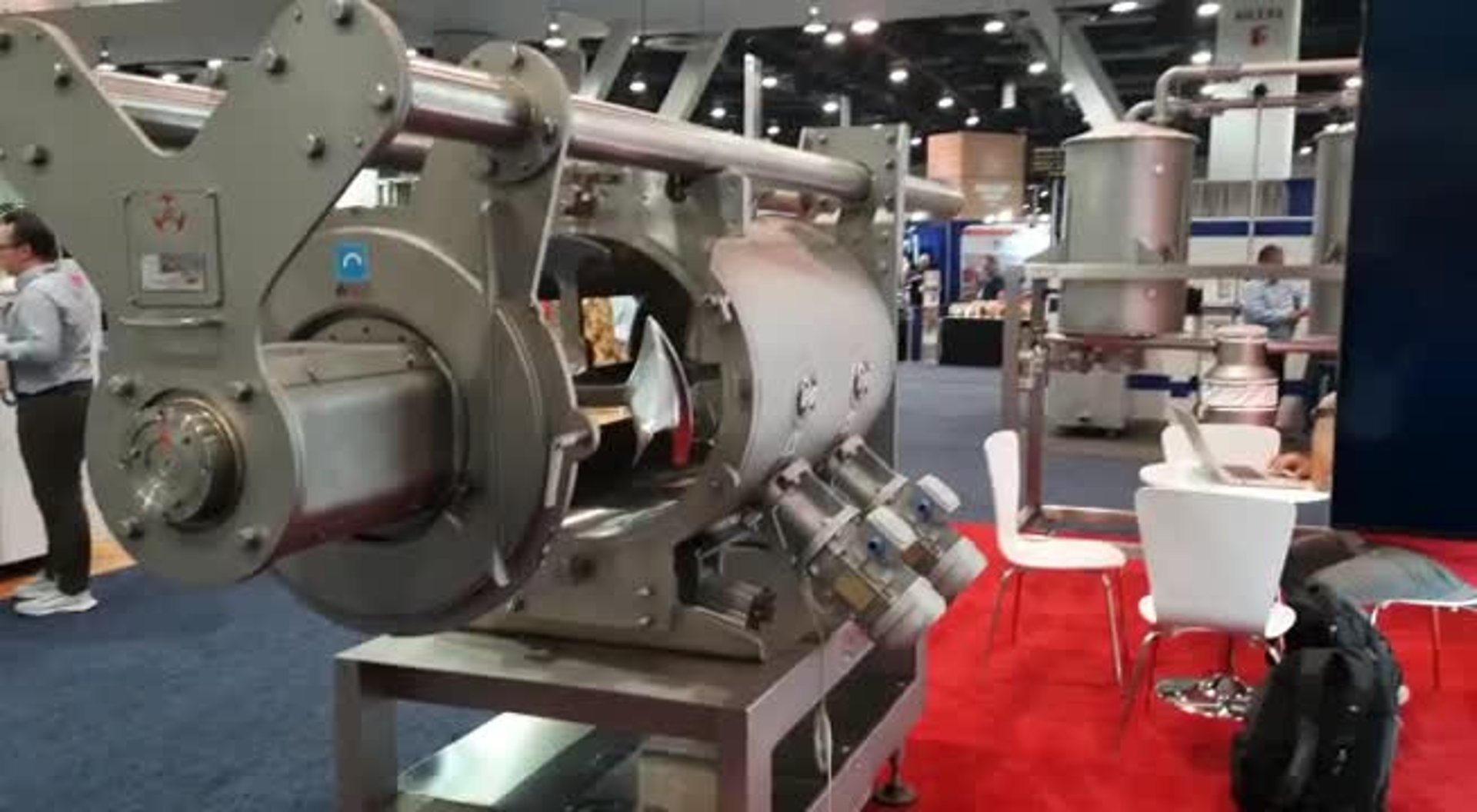
Powder and bulk solids mixers for industrial applications.
Explore our range of powder and bulk solids mixers, engineered for precision and reliable performance in diverse industrial applications.
Micromix: Your local partner for Mix Srl industrial mixing solutions.
MiX Srl offers innovative industrial mixing solutions with patented technologies, specializing in horizontal single shaft mixers, ribbon blenders, and twin shaft paddle mixers. Known for its expertise, MIX Srl provides unparalleled customer support and technical solutions with clear advantages in performance and cost-efficiency.
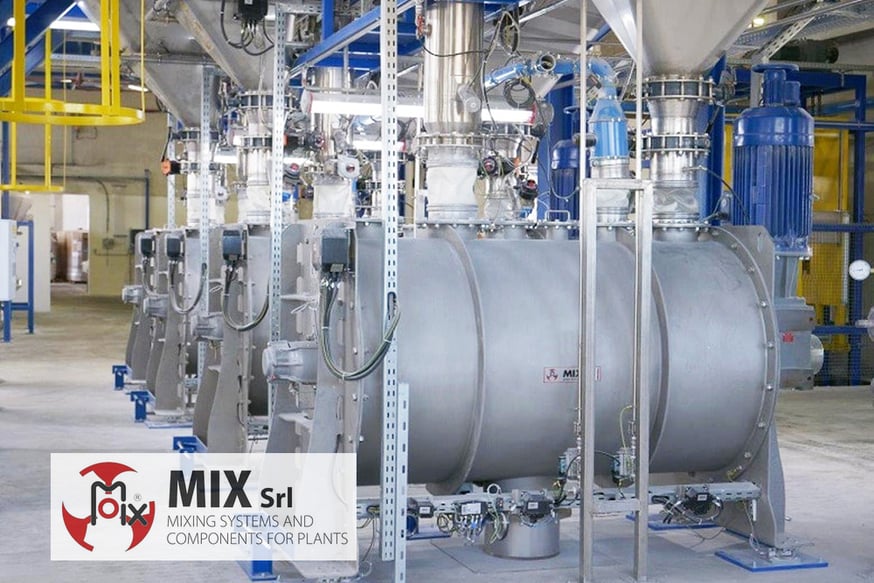
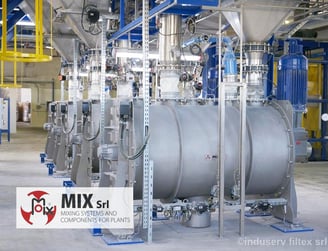
MiX Srl – Industrial Mixing Technology Experts
Versatile, High-Capacity Mixing Solutions
Mix Srl offers a comprehensive range of industrial solutions, including mixers, reactors, vacuum dryers, granulators, and more, with capacities ranging from 2 liters to 50,000 liters. As a partner of Mix Srl, Micromix provides both batch and continuous mixing options designed for atmospheric, vacuum, and pressurized environments, as well as with heat exchangers. These solutions are tailored to meet diverse processing needs, ensuring efficiency, reliability, and high performance.
MXA Ploughshare
MXH PalaMix
Continuous Single Shaft Industrial Mixers
Reliable, High-Quality Mixing with Consistent Output
Hourly Productivity: 500 to 1,200,000 liters/h
Mixing Chamber: Cylindrical design
Mixing Tools: Ploughshare, Ploughshare with toothed design, Mix Paddle, Mix Paddle with toothed design
Materials of Construction: Carbon steel, Hardox 450, AISI 304, AISI 316, AISI 316Ti
Inspection Door: Complete with safety electric lock
Discharge Door: Vertical, adjustable internal diaphragms for regulating production capacity
Rotor Shaft: Turned and coaxial ends
Mixing Time: Adaptable to specific processes
Mixing Quality: Extremely high and consistent output quality
Rotor Shaft Sealing: Packing seals and wear-resistant ferrules, prepared for flushing with air/nitrogen
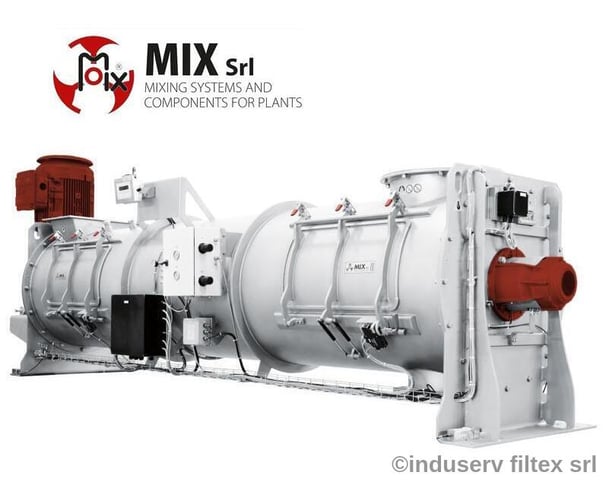
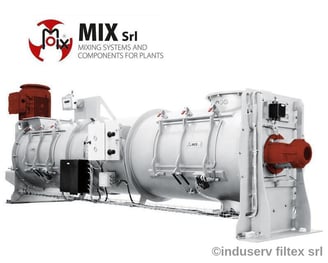
Technical Specification
Explore our detailed product specifications and enhance your technical understanding of equipment for handling and mixing powders, bulk solids, and liquids in industrial applications.
Mix Srl MXA Ploughshare and MXH PalaMix Continuous Mixers with Ploughshare or PalaMix mix paddles Tools
In a continuous process, the machine operates as an open system. The production sequence involves the product entering through the loading inlet, being mixed, and exiting via the unloading outlet. Both ports remain open throughout. However, the quality of the finished mixture is influenced by the time the product spends in the mixing chamber and the volume being processed.
Benefits
Adaptable Mixing Time: Mixing time can be tailored to meet the specific needs of the process, ensuring optimal blending and performance.
High Mixing Quality: Provides exceptional and homogeneous mixing quality, crucial for high-precision applications.
Consistent Product Output: Ensures that the product output maintains constant quality and uniformity, with a low coefficient of variation (CV ≤ 3%).
Low Maintenance: The design ensures minimal maintenance and long-lasting operation with reduced downtime.
High Productivity: Offers impressive hourly productivity, ranging from 500 to 1,200,000 liters per hour, making it suitable for both small and large-scale production.
Available Options Upon Request
Food-Grade Declaration: Compliance with EU regulations 1935/2004 EC and 2023/2006 EC for food contact.
Atex Compliance: Declaration of conformity for Atex II 1/3D Ex h IIIB T135°C Da/Dc (Inside Zone 20, Outside Zone 22), suitable for explosive environments.
Wolfram Carbide Coating: On mixing tools for added durability and resistance to wear.
Liquid Injection System: Allows precise addition of liquids during the mixing process.
High-Speed Choppers / Homogenizers: Side-mounted for efficient breaking down and homogenization of materials.
Pneumatic Sampler: For easy sampling of materials during operation.
Pneumatic Panel: Provides seamless control over mixer functions.
Heat Exchanger: Integrated into the mixing chamber to control heating or cooling during processing.
Frontal Discharge Door: Adjustable slide gate for optimized discharge control.
Pneumatic Cleaning System: Ensures easy and efficient cleaning of the mixing chamber.
Lip Seal with Air Flushing: Additional sealing protection for enhanced system performance.
Custom Finishes: Various finishes available for parts in contact with the product to meet specific application requirements.
Technical Specifications
Description
The Mix Srl Continuous Mixer MXA Ploughshare and MXH PalaMix are designed for efficient mixing of powders, granules, flakes, fibers, pastes, and liquids. It can handle a wide range of production processes including granulation, wetting, film coating, and temperature regulation (heating and cooling). It ensures high-quality, consistent mixing for industrial applications with high demands on product uniformity.
Function
The Mix Srl Continuous Mixer MXA Ploughshare and MXH PalaMix utilizes a cylindrical mixing chamber where the material is moved through by specialized mixing tools such as ploughshares or mix paddles. The system offers adjustable mixing times to suit various processes. It also ensures uniform distribution of liquids and powders for applications such as granulation and film coating. The mixer is capable of managing continuous processing, enabling high throughput for large-scale production.
These mixers are perfect for blending powders, granules, flakes, fibers, and pastes, wetting solids with liquids, granulating with binding liquids, film coating, and maintaining temperature through heating or cooling.
Features
Hourly Productivity: From 500 to 1,200,000 liters per hour depending on material and process requirements.
Mixing ratio 1/100.000
Coefficient of variation (CV): ≤ 3 %
Mixing Chamber: Cylindrical design for high-efficiency mixing.
Mixing Tools: Ploughshare, ploughshare with toothed design, mix paddle, mix paddle with toothed design.
Material of Construction: Carbon steel, Hardox 450, AISI 304, AISI 316, and AISI 316Ti for optimal durability.
Inspection Door: Equipped with a safety electric lock for secure operation.
Discharge Door: Vertical discharge with adjustable internal diaphragms for capacity regulation.
Rotor Shaft: Coaxial ends with robust sealing system using packing seals and wear-resistant ferrules. Can be flushed with air or nitrogen.
Sealing System: Enhanced sealing with wear-resistant ferrules for extended service life.
...for more questions and specifications regarding industrial mixers and equipment for handling powders, bulk solids and liquids.
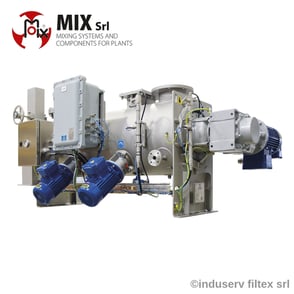
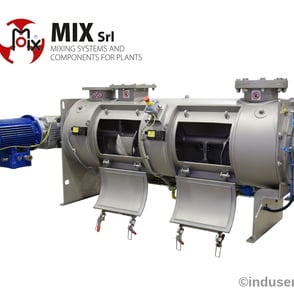
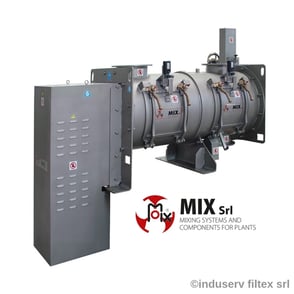
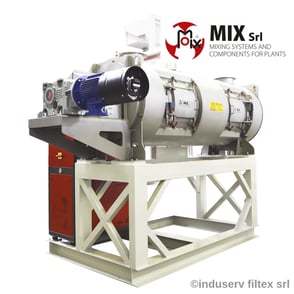
MXC Ploughshare
MXK PalaMix
Efficient batch mixing using Ploughshare or PalaMix tools
Optimal material blending and consistent results across various applications.
Batch size: 65 to 28,000 liters (net)
Cylindrical mixing chamber
Mixing tools: Ploughshare, Mix Paddle (toothed options)
Materials: Carbon steel, Hardox 450, AISI 304/316/316Ti
Discharge door: Round profile with electric safety lock
Rotor shaft: Coaxial ends, sealed with wear-resistant ferrules
Short mixing time
High mixing quality
Repeatable batch results
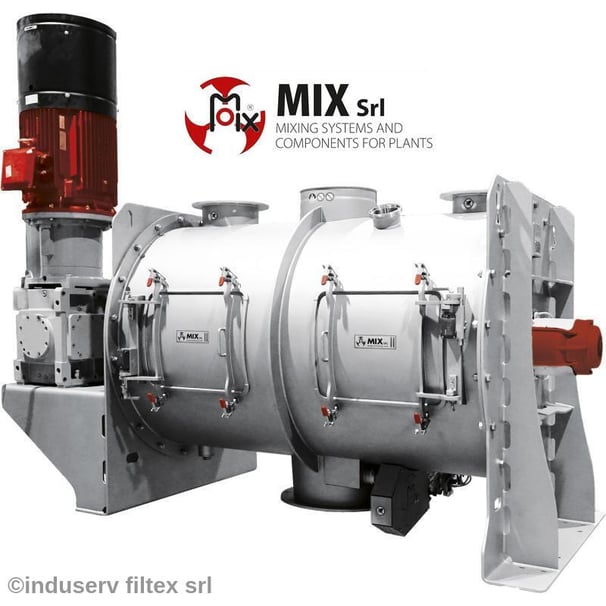
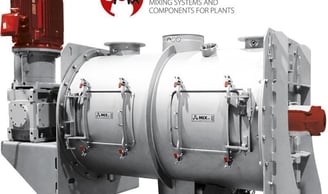
Technical Specification
Explore our detailed product specifications and enhance your technical understanding of equipment for handling and mixing powders, bulk solids, and liquids in industrial applications.
The Mix Srl Batch Mixers MXC Ploughshare and MXK PalaMix with Ploughshare or PalaMix mix paddles Tools
For batch processes, which involve discontinuous production, the simplified sequence begins with the air venting outlet remaining open, releasing air into a filter or preferably under slight depression. The product is then loaded while the unloading port remains closed. During mixing, the unloading port stays closed, and the loading port is either closed or open if connected to a closed feeding hopper. Finally, the mixture is unloaded through the open unloading port.
Benefits
Adaptable Mixing Time: Tailorable mixing time for specific processes, ensuring optimal blending and performance.
High Mixing Quality: Guarantees exceptional, homogeneous mixing, essential for precision applications.
Repeatable Batch Results: Consistent results across batches, offering reliable performance for large-scale production.
Consistent Product Output: Ensures consistent quality and uniformity in product output with a low coefficient of variation (CV ≤ 3%).
Low Maintenance: Designed for easy maintenance and minimal downtime, ensuring continuous operation.
High Productivity: Capable of processing large batch sizes, ranging from 65 to 28,000 liters, making it ideal for both small and large-scale production needs.
Available Options Upon Request
Food-Grade Declaration: Compliance with EU regulations 1935/2004 EC and 2023/2006 EC for food contact.
Atex Compliance: Declaration of conformity for Atex II 1/3D Ex h IIIB T135°C Da/Dc (Inside Zone 20, Outside Zone 22), suitable for explosive environments.
Wolfram Carbide Coating: On mixing tools for added durability and wear resistance.
Liquid Injection System: Allows precise addition of liquids during the mixing process for accurate product consistency.
High-Speed Choppers / Homogenizers: Side-mounted for efficient breakdown and homogenization of materials during mixing.
Pneumatic Sampler: Provides easy sampling of materials during operation to monitor product quality.
Pneumatic Panel: Integrated control panel for seamless operation and monitoring of mixer functions.
Heat Exchanger: Integrated into the mixing chamber to control the heating or cooling of materials during processing.
Big Bomb Door: A large discharge door along the entire length of the mixing chamber for fast, nearly residue-free discharge.
CIP Cleaning System: Pre-disposition for Cleaning in Place (CIP) systems, enabling efficient and hygienic cleaning.
Pneumatic Cleaning System: Ensures easy and efficient cleaning of the mixing chamber between batches.
Lip Seal with Air Flushing: Provides enhanced sealing protection to improve system performance and reduce downtime.
Custom Finishes: Parts in contact with the product are available with customized finishes to meet specific application requirements.
Technical Specifications
Description
The Mix Srl Batch Mixers MXC Ploughshare and MXK PalaMix are designed to efficiently mix a wide variety of materials, including powders, granules, flakes, fibers, pastes, and liquids. These mixers are ideal for processes such as granulation, wetting of solids, film coating, and temperature regulation (heating and cooling). They are specifically built for batch (discontinuous) production processes, ensuring consistent, high-quality mixing suitable for industries with high demands for product uniformity.
Function
The Mix Srl Batch Mixers MXC Ploughshare and MXK PalaMix feature a cylindrical mixing chamber where materials are mixed using specialized tools such as ploughshares or mix paddles. The system offers flexible mixing times to accommodate various processing needs. It ensures uniform distribution of liquids and powders, making it ideal for applications like granulation, film coating, and the wetting of solids. The mixer supports batch processing, enabling repeatable, high-quality production for a wide range of materials.
Batch mixers are typically used for:
Mixing powders, granules, flakes, fibers, and pastes
Wetting of solids with one or more liquids
Granulation by injecting binding liquids
Film coating by applying liquid on powder, followed by adding another powder
Heating /cooling / temperature keeping
Features
Hourly Productivity: Batch sizes ranging from 65 liters to 28,000 liters (net), depending on material and process requirements.
Mixing Ratio: 1/100,000, ensuring high precision.
Coefficient of Variation (CV): ≤ 3%, ensuring consistent product output.
Mixing Chamber: Cylindrical design optimized for high-efficiency mixing.
Mixing Tools: Ploughshare, ploughshare with toothed design, mix paddle, mix paddle with toothed design.
Materials of Construction: Carbon steel, Hardox 450, AISI 304, AISI 316, AISI 316Ti for excellent durability and wear resistance.
Inspection Door: Equipped with a safety electric lock for secure operation.
Discharge Door: Round-profile discharge door integrated into the mixing chamber’s bottom for efficient unloading.
Rotor Shaft: Coaxial ends with robust sealing systems using packing seals and wear-resistant ferrules. Designed for flushing with air or nitrogen.
Sealing System: Enhanced sealing with wear-resistant ferrules to protect the rotor shaft and extend service life.
...for more questions and specifications regarding industrial mixers and equipment for handling powders, bulk solids and liquids.
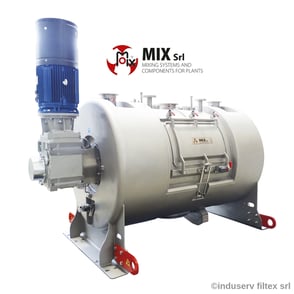
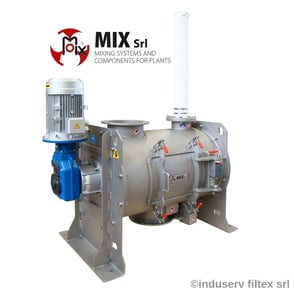
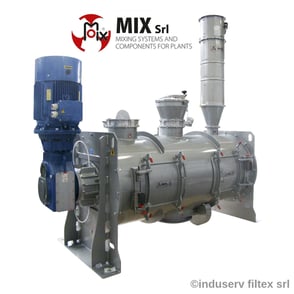
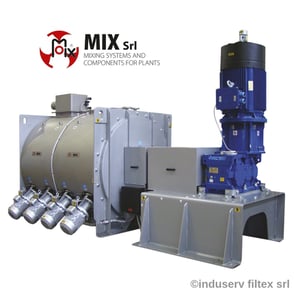
MXC / MXK Batch Series with EXTRACTABLE Rotor Shaft
Efficient batch mixing using Ploughshare or PalaMix tools
Batch mixing with extractable rotor shaft for easy cleaning.
Batch Size: 65 to 28,000 liters (net).
Short Mixing Time: Fast cycle for increased efficiency.
Low Maintenance: Designed for minimal upkeep.
Easy Deep Cleaning: Simple to clean for hygiene and process changes.
High Mixing Quality: Ensures uniform and consistent results.
Repeatable Batches: Delivers reliable outcomes for each batch.
Mixing Ratio: 1/100,000 for precise results.
Coefficient of Variation (CV): ≤ 3% for minimal variation.
Mixing Chamber: Cylindrical design for efficient blending.
Mixing Tools: Ploughshare, toothed ploughshare, mix paddle, and toothed mix paddle.
Materials: Carbon steel, Hardox 450, AISI 304/316/316Ti for durability.
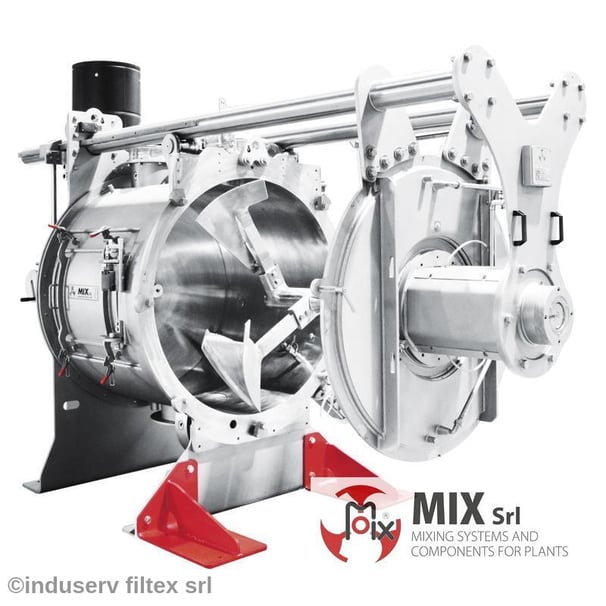
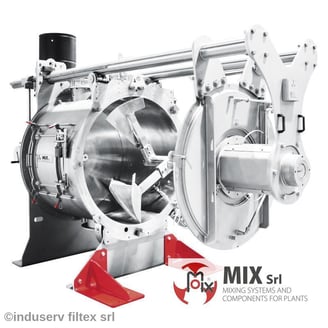
Technical Specification
Explore our detailed product specifications and enhance your technical understanding of equipment for handling and mixing powders, bulk solids, and liquids in industrial applications.
The Mix Srl Extractashaft Batch Mixers, featuring the MXC Ploughshare and MXK PalaMix models with Ploughshare or PalaMix mix paddle tools, are equipped with a fully extractable rotor shaft mounted on sliding support arms.
This design provides easy access to all areas inside the mixing chamber, allowing for thorough cleaning of the mixer, rotor shaft, and mixing tools. This solution is ideal for industries that require frequent cleaning and efficient mixing with every recipe change.
Benefits
Repeatable Results: Consistent, high-quality batches for each production cycle.
Easy Cleaning: Full access to all areas for quick and effective cleaning, essential for frequent recipe changes.
High Mixing Quality: Ensures uniformity and precision in mixing with minimal variation.
Increased Productivity: Short mixing time and easy maintenance lead to higher throughput and less downtime.
Minimal Wear and Tear: Durable materials and sealing systems extend the operational life of the mixer.
Available Options Upon Request
Food-Grade Compliance: Declaration of conformity with regulations 1935/2004 EC and 2023/2006 EC for food contact.
ATEX Compliance: Declaration for Atex II 1/3D Ex h IIIB T135°C Da/Dc (Inside Zone 20, Outside Zone 22) for explosive environments.
Wolfram Carbide Coating: Enhances durability and wear resistance of mixing tools.
Liquid Injection System: Precise addition of liquids during mixing.
Side-Mounted High-Speed Choppers/Homogenizers: For efficient particle size reduction and material homogenization.
Pneumatic Sampler: Easy sampling of materials during production.
Pneumatic Panel: Provides seamless control over mixer functions.
Heat Exchanger: Integrated for precise temperature regulation during mixing processes.
Big Bomb Door: Full-length discharge door for almost residue-free unloading.
CIP Cleaning System: Pre-disposition for Clean-In-Place (CIP) cleaning system.
Pneumatic Cleaning: For efficient cleaning of the mixing chamber.
Lip Seal with Air Flushing: Additional sealing for improved protection and performance.
Custom Finishes: Available upon request for parts in contact with the product.
Technical Specifications
Description
The Mix Srl Batch Mixers Extractashaft MXC Ploughshare and MXK PalaMix with extractable rotor shaft offers an innovative solution for various production processes. It allows easy access to all parts of the mixing chamber, facilitating thorough cleaning of the mixer, rotor shaft, and tools. Ideal for industries that require frequent cleaning and product changeover, this mixer is designed to ensure high-quality, consistent results.
Function
The Mix Srl Batch Mixers Extractashaft MXC Ploughshare and MXK PalaMix operates with a completely extractable rotor shaft mounted on sliding support arms, providing full access for cleaning and maintenance. It is used for mixing powders, granules, flakes, fibers, and pastes, as well as for applications such as wetting, granulation, and film coating. The system can also be equipped for heating, cooling, and temperature control during the mixing process.
Batch mixers are typically used for:
Mixing powders, granules, flakes, fibers, and pastes
Wetting of solids with one or more liquids
Granulation by injecting binding liquids
Film coating by applying liquid on powder, followed by adding another powder
Heating /cooling / temperature keeping
Features
Batch Size: 65 to 28,000 liters (net) for flexible production.
Cylindrical Mixing Chamber: Ensures efficient and uniform mixing.
Mixing Tools: Options include ploughshare, ploughshare with toothed design, and mix paddle with toothed design for different process needs.
Materials of Construction: Carbon steel, Hardox 450, AISI 304, AISI 316, AISI 316Ti for durability and resistance.
Extractable Rotor Shaft: Easy access to mixing chamber for complete cleaning and maintenance.
Inspection Door: Equipped with a safety electric lock for secure operation.
Discharge Door: Round profile with integrated bottom discharge for efficient unloading.
Rotor Shaft Sealing: Features packing seals and wear-resistant ferrules with air/nitrogen flushing capability.
Mixing Time: Short mixing cycle to optimize production.
Low Maintenance: Designed for minimal downtime and easy upkeep.
...for more questions and specifications regarding industrial mixers and equipment for handling powders, bulk solids and liquids.
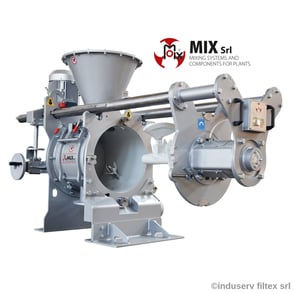
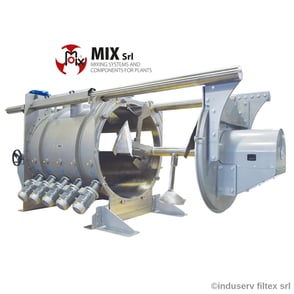
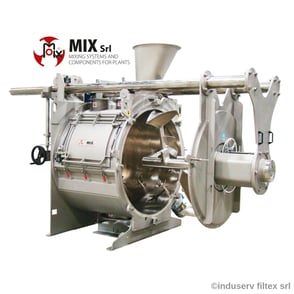
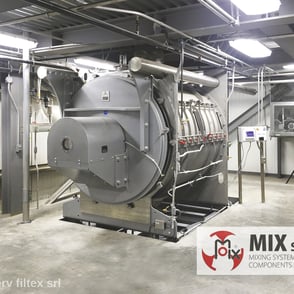
Li-ion MIX
Li-ion MIX mixers specifically designed for the production of battery masses
One of the biggest challenges over the past decade has been maintaining sustainable growth while preserving the resources of our planet.
Forecasts predict a 50% increase in energy consumption by 2050, which necessitates a significant technological leap in battery production.
MIX Srl is addressing this technological evolution with a specialized team that has developed a range of Li-ion MIX mixers specifically designed for the production of battery materials.
The Li-ion Mix range builds on over 30 years of expertise in the field of powder mixing, offering a solid foundation of knowledge and experience.
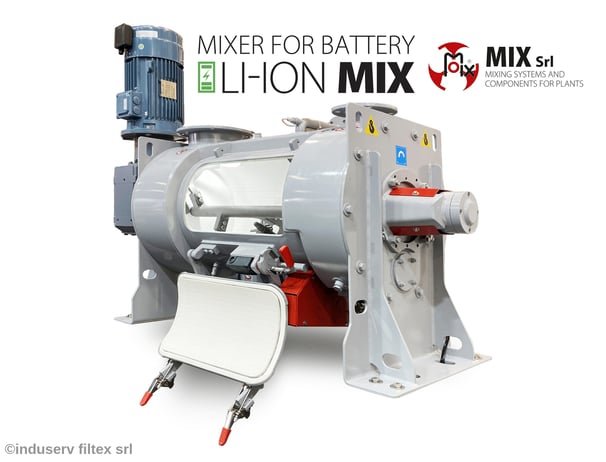
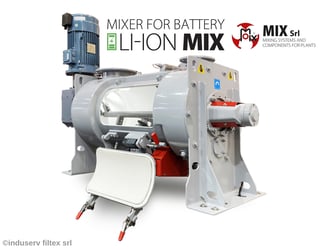
Technical Specification
Explore our detailed product specifications and enhance your technical understanding of equipment for handling and mixing powders, bulk solids, and liquids in industrial applications.
Prevent dust leakage, as certain ingredients in the compounds may be toxic or hazardous.
The rotor shaft seals of the Li-ion Mix series are designed to ensure an airtight seal and minimize wear caused by dust. These are radial seals without packing, with sealing maintained by a pressurized air barrier.Ensure perfect homogenization.
The inclusion of side choppers guarantees efficient dispersion of micro-additives in the shortest possible time.
Li-ion Mix – continuously evolving to meet today’s challenges.
Technical Specifications
In lithium-ion battery production, it is crucial to:
Prevent contamination of raw materials to ensure high battery quality.
The mixing chamber of the Li-ion Mix is typically lined with ceramic tiles based on alumina, which are secured using a two-component epoxy resin.
Due to the complex geometry of the equipment, the rotor shaft and mixing ploughshares can be coated with:
Two-component epoxy resin infused with ceramic powder
Thermal spray coating with alumina oxide (plasma spray)
Thermal spray coating with tungsten carbide (HVOF)
For specialized requirements, alternative coatings such as ETFE and ECTFE are also available.
...for more questions and specifications regarding industrial mixers and equipment for handling powders, bulk solids and liquids.
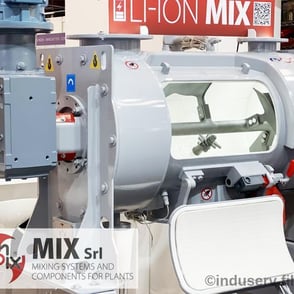
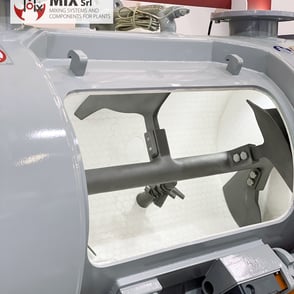
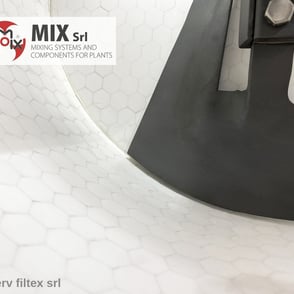
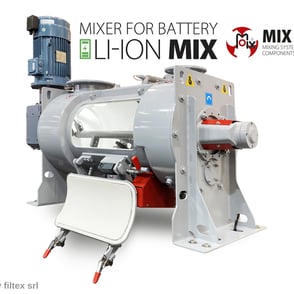
MXN Four Ribbon
Mixing Of Batches With 4-Ribbon-Mixers
Keeping the product in movement through efficient mixing, wetting, and precise heating/cooling processes
Batch Size: 80 to 35,000 liters (net).
Mixing Chamber: U-shaped for efficient mixing.
Mixing Tools: Four opposing ribbons for thorough blending.
Materials: Carbon steel, Hardox 450, AISI 304/316/316Ti.
Short Mixing Time: Fast cycle for higher productivity.
High Mixing Quality: Ensures consistent, uniform mixing.
Repeatable Batches: Consistent results for every batch.
Gentle Mixing: Minimizes material damage.
Low Maintenance: Designed for easy upkeep.
Inspection Door: Safe, accessible top cover with electric lock.
Rotor Shaft Sealing: Durable seals with air/nitrogen flushing.
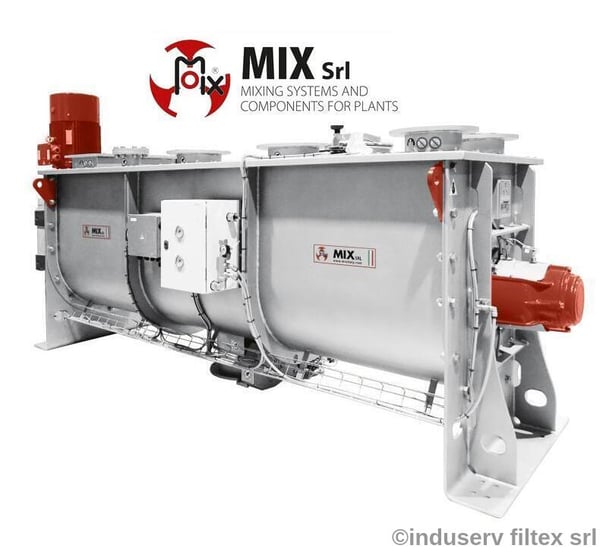
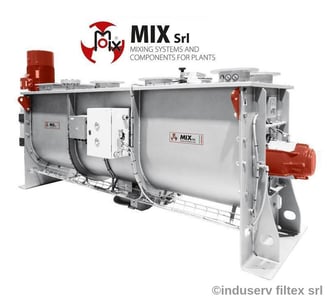
Technical Specification
Explore our detailed product specifications and enhance your technical understanding of equipment for handling and mixing powders, bulk solids, and liquids in industrial applications.
The Mix Srl MXN Four Ribbon Mixer is designed for batch processes, meaning discontinuous production. The simplified production sequence involves the following steps: The air venting outlet remains open, allowing air to be released into a filter or, ideally, under slight depression. The product is loaded into the mixing chamber while the unloading port remains closed. Mixing occurs with the unloading port closed, and the loading port can either be closed or open if connected to a closed feeding hopper. Finally, the mixture is unloaded through the open unloading port.
Technical Specifications
Description
The Mix Srl MXN Four Ribbon Mixer is designed for batch processes, offering an efficient and versatile solution for mixing powders, granules, flakes, fibers, pastes, and liquids. With its specialized four-ribbon mixing system, this machine guarantees high-quality, consistent results while being suitable for applications requiring gentle handling, temperature control, and liquid addition. The mixer is perfect for industries where precise, repeatable batch results are essential.
Function
The MXN Four Ribbon Mixer features a "U"-shaped mixing chamber that uses four ribbons arranged in opposing pairs for effective material movement. The mixing process is initiated by loading the product, and the mixer operates with the unloading port closed to ensure efficient blending. The air venting outlet is always open to release air into a filter or slight depression, ensuring that dust or unwanted particles are minimized during operation. The mixer can also be used for heating, cooling, or maintaining the temperature of the product, making it ideal for temperature-sensitive processes.
Features
The MXN Four Ribbon Mixer boasts several key features that make it suitable for a wide range of industrial applications:
Batch size: From 80 to 35,000 liters (net), offering flexibility in production volumes.
Mixing Chamber: "U" shaped design for optimal material flow and efficiency.
Mixing Tools: Four ribbons, opposing two by two, for gentle and thorough mixing.
Material of Construction: Carbon steel, Hardox 450, AISI 304, AISI 316, and AISI 316Ti for durability and resistance to wear.
Inspection Door: Equipped with safety grid and electric lock for secure operation.
Discharge Door: Round profile that forms the bottom of the mixing chamber for efficient discharge.
Rotor Shaft: Coaxial ends with robust sealing system, prepared for flushing with air/nitrogen.
Benefits
Short Mixing Time: Enables quick, efficient mixing while maintaining high quality.
High Mixing Quality: Ensures uniform distribution of materials, crucial for applications requiring consistent results.
Repeatable Results: Capable of producing consistent batches with minimal variation.
Gentle Mixing: The gentle action of the ribbons preserves the integrity of sensitive materials.
Low Maintenance: Designed for ease of maintenance, reducing downtime and extending operational lifespan.
Available Options Upon Request
Food-Grade Declaration: Compliance with EU regulations 1935/2004 EC and 2023/2006 EC for food contact.
Atex Compliance: Declaration of conformity Atex II 1/3D Ex h IIIB T135°C Da/Dc (Inside Zone 20, Outside Zone 22) for use in explosive environments.
Wolfram Carbide Coating: On the external profile of the mixing ribbon for enhanced durability and wear resistance.
High-Speed Choppers/Homogenizers: Side-mounted for efficient breakdown and homogenization of materials.
Pneumatic Sampler: For easy sampling of the product during mixing.
Pneumatic Panel: Seamless control of mixer functions through a pneumatic interface.
Heat Exchanger: Integrated into the mixing chamber to provide heating or cooling during the process.
Big Bomb Door: Spanning the length of the mixing chamber for near residue-free discharge in the shortest time.
CIP Cleaning System: Predisposition for easy and efficient cleaning.
Pneumatic Cleaning: Ensures efficient cleaning of the mixing chamber.
Lip Seal with Air Flushing: Additional protection for the sealing system.
Custom Finishes: Various finishes available for parts in contact with the product, tailored to specific application needs.
Inspection Door: Easy access to the mixing chamber with a safety electric lock for secure operation.
...for more questions and specifications regarding industrial mixers and equipment for handling powders, bulk solids and liquids.
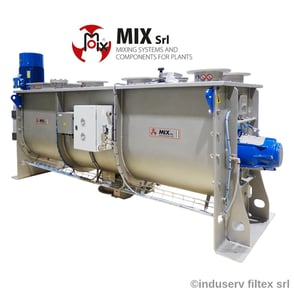
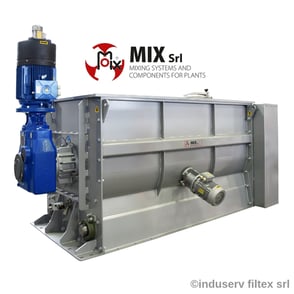
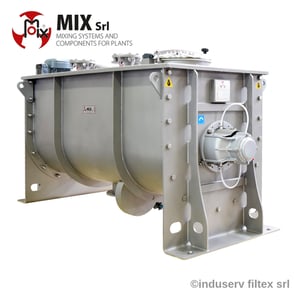
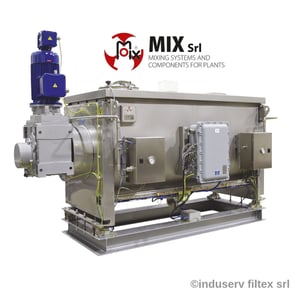
WBN Series
Tubular Batch-Type Industrial Ribbon Blenders
The WBN model keeps mixtures homogeneous, ideal for a wide range of materials and batch sizes.
Capacity: 10 ~ 20,000 litres per batch
Mixing time: 5 ~ 15 min
End bearing assemblies with air or nitrogen-purged shaft seals or grease sealing
Heavy-duty mixing chamber made from carbon steel or 304L / 316L stainless steel
Stainless steel surface finish: grit silking, mirror polishing, glass bead blasting
Large hopper inlet or multiple round inlet spouts
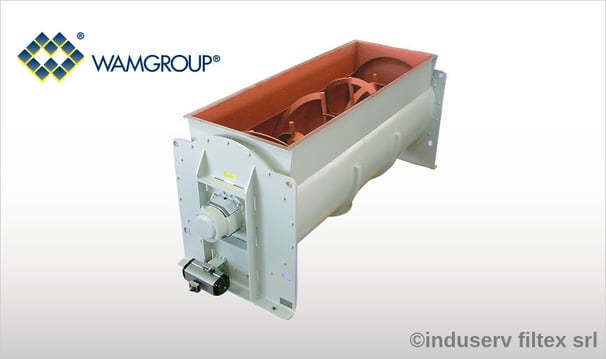
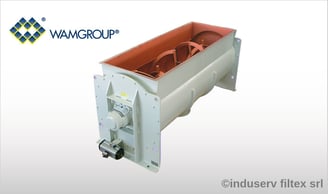
Technical Specification
Explore our detailed product specifications and enhance your technical understanding of equipment for handling and mixing powders, bulk solids, and liquids in industrial applications.
WBR Industrial Ribbon Blenders provide an optimal solution, meeting market demands for quality, ease of maintenance, and advanced mixing technology. Thanks to the use of proven standard components, MAP® can offer an attractive price without compromising quality.
Technical Specifications
Description
Batch-type WBN Industrial Ribbon Blenders feature a horizontal, single-shaft double counter-pitch ribbon screw housed within a tubular mixing drum. The design includes a central or rectangular inlet port running the full length of the drum, a central discharge outlet, a venting spout, and two end plates with integrated air or gas-purged shaft seals. The system is powered by a drive unit with complete power transmission.
Function
The outer ribbon moves the material from both ends of the vessel toward the center, while the inner ribbon directs it toward both ends, creating a convective mixing action. This results in gentle processing of the product within a relatively short mixing time.
Typically, Batch-type WBN Industrial Ribbon Blenders are used for mixing dry PVC, powders, granules, as well as liquids and low-viscosity pastes.
Features
Capacity: 10 ~ 20,000 litres per batch
Mixing time: 5 ~ 15 min
End bearing assemblies: Air or nitrogen-purged shaft seals or grease sealing options
Heavy-duty mixing chamber: Made from carbon steel or 304L / 316L stainless steel
Stainless steel surface finishes: Grit silking, mirror polishing, or glass bead blasting
Inlet options: Large hopper inlet or multiple round inlet spouts
Benefits
Low maintenance
Durable machine
Power rating: Adapted to the specific application
Mixing expertise: Access to know-how and test facilities
Available Options Upon Request
Additional liquid supply equipment
Pneumatic sampling device
Pneumatic control panel
Jacketed mixing chamber for heating or cooling
Industry Sectors and Applications
Explore the diverse industry sectors and applications where our products provide reliable, efficient, and cost-effective solutions.
From manufacturing and agriculture to specialized industrial equipment, the wide range of high-quality products and solutions supplied by Micromix is designed to meet the unique demands of each sector, ensuring optimal performance and versatility.
Building & Construction: DryMix Building Materials Processing, Chemical Ad-Mixtures for Building & Construction, Brick & Roof Tile Production, Marble Processing
Feed & Food: Animal Feed Milling, Animal Feed Additives Processing, Fish Food Production, Pet Food Processing, Biscuit Processing
Plastics & Chemicals: Plastics Raw Material Processing, Rubber Processing, Rubber & Plastics Recycling, Fertilizer, Pesticide, and Insecticide Processing, Pharmaceutical Processing, Paint, Varnish, and Resin Processing
Heavy Industries: Cement, Lime, Gypsum, Minerals, and Refractory Products Processing, Crushing, Mining, Quarrying, Screening, and Micronizing Plants, Oil & Gas Extraction, Foundries, Iron and Steel Mills, Coking Plants, Power Plants (Fly-Ash Handling)
Renewable Energy: Biomass & Biogas Digestate from Organic Household Waste, Wood Biomass in Chip Form
Plants & Machinery: Lime Dosing, Dosing Plants, Mixing Plants, Packaging Plants, Battery Production, Wood or Cork Working Machinery, Tobacco Processing
Environmental Technology: Industrial Wastewater Treatment (including Sludge Treatment), Abattoirs (Slaughterhouses), Beverage Industry Wastewater, Food Processing & Catering Wastewater, Fruit & Vegetable Processing Wastewater, Pulp & Paper Processing, Starch & By-products Processing, Tanneries, Dyeing Works, Plastics Recycling Industry Wastewater, Municipal Wastewater Treatment (including Sludge Treatment), Industrial Solid Waste Handling & Treatment, Animal By-products Handling & Processing
Building & Construction: Mixing and blending of dry building materials, Chemical admixtures for concrete and mortar, Tile and brick production blending, Marble processing and mixing
Feed & Food: Animal feed mixing and additives incorporation, Fish food production and ingredient blending, Pet food mixing and supplement incorporation, Biscuit and bakery products mixing
Plastics & Chemicals: Blending of raw materials for plastic production, Rubber processing and additives incorporation, Recycling of plastics and rubber materials, Fertilizer, pesticide, and insecticide mixing, Pharmaceutical ingredient blending, Resin, paint, and varnish production
Heavy Industries: Cement, lime, gypsum, and mineral processing, Raw material and micronizing blending for mining industries, Fly ash handling in power plants, Steel, iron, and coking plant material blending
Renewable Energy: Biomass & Biogas digestate processing, Wood biomass processing in chip form
Plants & Machinery: Lime dosing for chemical applications, Integration into dosing, mixing, and packaging plants for various products, Wood and cork processing and tobacco industry applications
Environmental Technology: Wastewater treatment and sludge processing, Treatment of industrial effluents from abattoirs and beverage industries, Fruit and vegetable waste water treatment, Pulp and paper processing waste management, Treatment of industrial waste and animal by-products
INDUSTRY SECTORS
APPLICATIONS
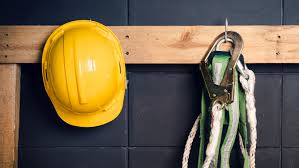
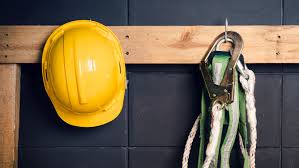
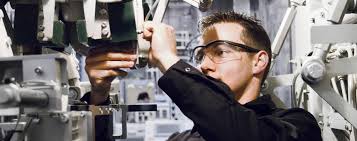
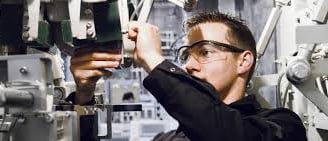
Product Features
Explore the key features of our product range, designed to ensure efficiency and reliability across a variety of applications.
Customer Success Stories
Explore customer experiences with our product range and innovative solutions, driving success across diverse industries.
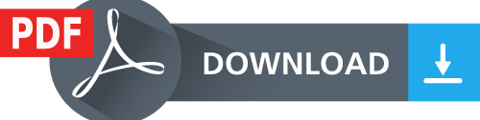
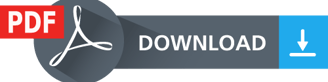


...for more questions and specifications regarding industrial mixers and equipment for handling powders, bulk solids and liquids.
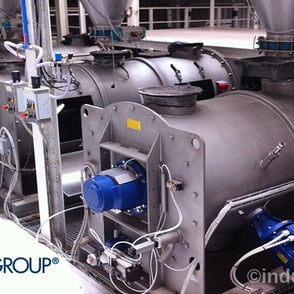

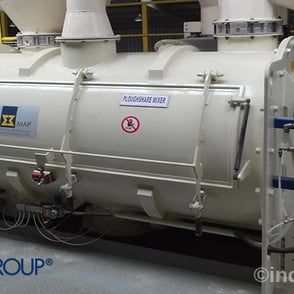
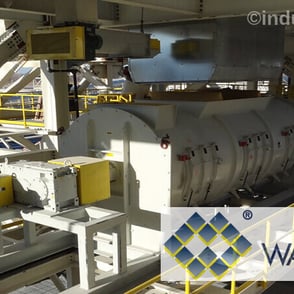
Explore More Products
You May Be Interested In
Peristaltic pumps
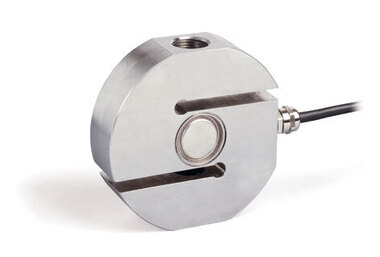
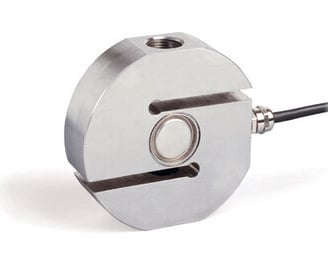
self-priming, reversibility, easy and quick maintenance and sterilization, no stress to the pumped liquid...
Peristaltic pump tubing
range of four different products to suit all possible applications and allows peristaltic pump users wide versatility with all chemicals...
Tension/compression load cell
ideal for tanks, hoppers, weighing belts, asphalt and concrete plants, force measurement...
Quality
Leading supplier of industrial mixers for efficiency.
© 2017 - 2025. All rights reserved.
iNDUSERV FiLTEX srl
Mon-Fri 8:30am - 18:00pm
Dependable and wear resistant components designed to withstand extreme conditions as: dust, temperature fluctuations, moisture, vibrations, and more.
Sustainability
Innovation
Modern manufacturing processes, combined with continuous product review and refinement, ensure that our processing equipment stays at the forefront of technology—delivering enhanced efficiency, simplified maintenance, and easier operation for you
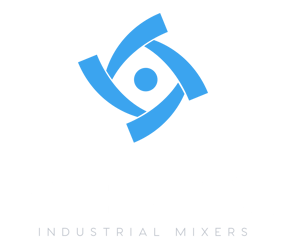
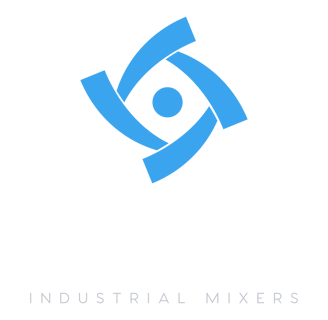

